Casting & Pouring
Gravity casting
Gravity casting is a process in which permanent molds are used and is sometimes called Permanent Mold Casting. In this process, a mold used to create the pattern for the part.
The mold is typically a permanent steel tool which is CNC machined to produce the pattern of the finished part. Molten material is poured by ladle into the mold. The mold can be heated or cooled based on specific needs and geometry of a part. When the part has frozen (set), the tool is opened and the part is removed. In this process, tools can have pins, cores, slides and other moving parts to create specific features.
Vulcan GMS can also use plaster tools and sand cores for some applications. Plaster or sand tooling allow for prototypes, low volume or some special geometry needs that can not be achieved with permanent steel tooling.
Vulcan offers insert tools for our multiple vertical and horizontal casting platforms. These are hydraulically driven allowing for faster cycling and better tolerance. This works well for various part sizes and can be completed with a lower total cost since the master tools are owned by Vulcan. As a customer, you are only in need of insert tooling. This is a hybrid process Vulcan has developed which is in between die casting and gravity casting, providing versatility to our customers.
Since Vulcan GMS is a full-service shop, we can cast and machine to achieve tighter tolerances, better surface finishes or key features. We are also able to use standard tools to create cast blocks in order to machine parts that reduce cost. Cast material costs less than lead plate so we can offer our customer options. Based on design needs, we can suggest the best process to meet your product needs.
Pouring
Pouring is a process in which molten lead is poured into a vessel such as a fabrication or transport cask. Vulcan can supply these types of products complete with the steel fabrication or the lead pour alone.
Vulcan is able to produce fabrications or machined assemblies that require lead pours for shielding. We are able to ladle fill or pump material into vessels and we can handle 1 to 20,000 pound pours. We frequently offer this type of service to the security and industrial X-ray industry.
Heat Treating and Preheating
Heat treating is a process in which heating elements are wrapped around a vessel (cask) in rows. Thermal relays are welded to vessel in specific areas. The temperature at those relays are sent back to a heat controller and monitored. This allows Vulcan to see and control the temperature by zone on the vessel before, during and after the pour.
Vessels are preheated to a defined temperature based on design, geometry and volume. This is a slow ramp up to limit warp of the vessel. Once up to the correct temperature, lead is poured in and maintained in a molten state after full pour. After the pour is complete, the unit is ready to begin the cooling phase. The rows of heaters are lowered and shut down at the specific rate from bottom up to ensure a solid fill and reduce the chances of porosity.
Preheating can also be done by oven warming, flame warming or running hot oil in a tool. Based on the needs, Vulcan will work with you to find the best solution.
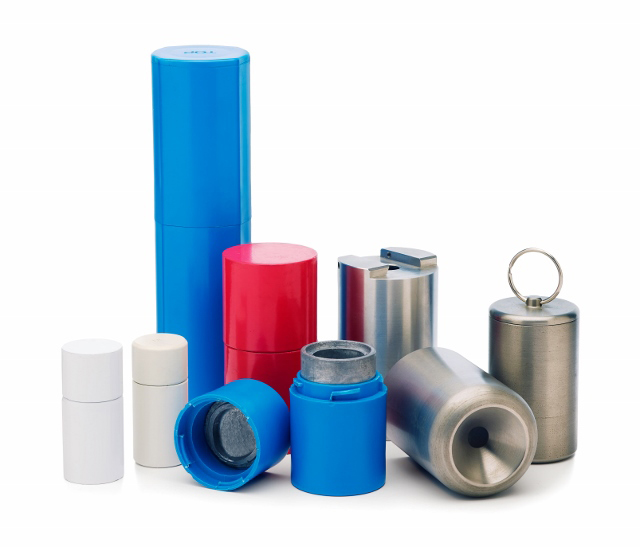

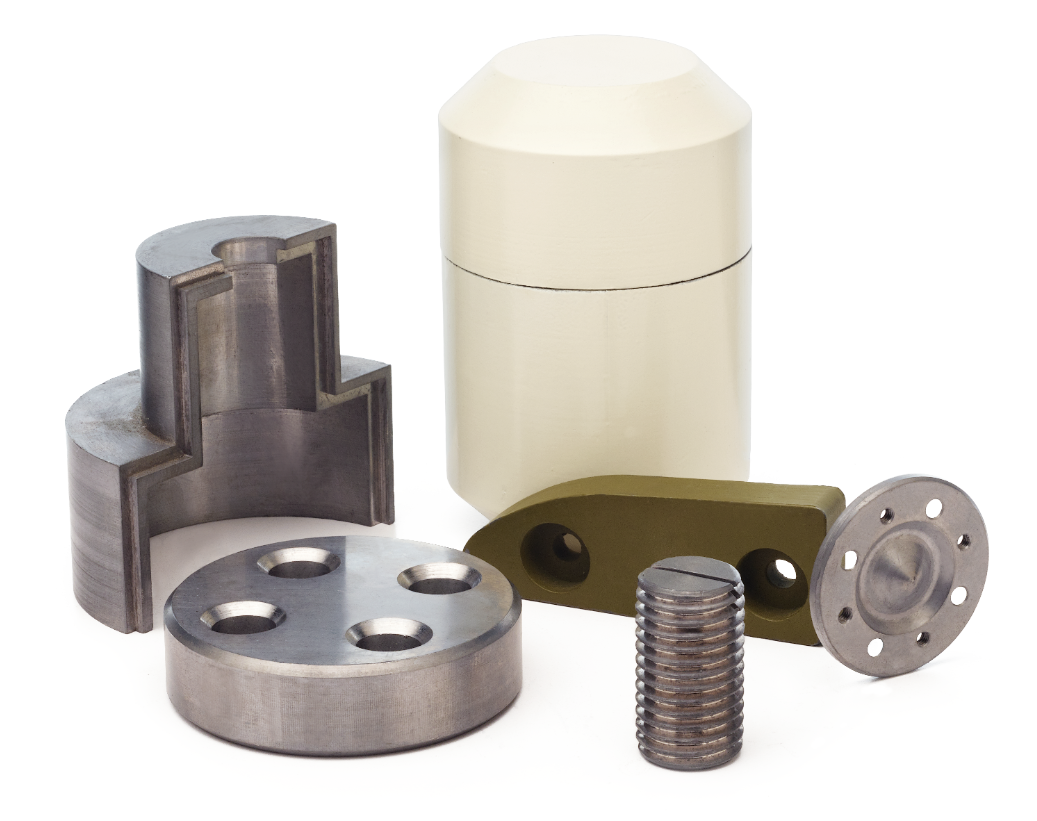